Inner Mongolia grass capital central kitchen system process description
Time:
2022-05-13
一(yī)、Basic overview of the ranch
1、Ranching for the time being to 5000 head of cattle scale.
2、The average feed intake of the whole herd is 160 tons/day (maximum 32KG/day per cow); (30% concentrate and 70% roughage for the whole diet) then 48 tons/day of concentrate and 112 tons/day of roughage are needed.
二、TMR preparation machine configuration calculation parameters
1、Diet weight is calculated according to 0.28T/m³ on average; the best mixing volume of TMR preparation machine is calculated according to 85%.
2. Each working cycle of TMR preparation machine is calculated according to 30 minutes.
3、The first feeding of each day is calculated as 50% of the whole day feeding volume, which is 80 tons.
4、The first feeding per day is calculated according to 3 hours, and the average feeding per hour is 26.7 tons.
5、The production capacity of 30 cubic TMR preparation machine is 14.56 tons per hour ( 30*0.28*0.85*2 tanks), two 30 cubic TMRs meet the requirements.
三、Concentrate and grass processing scale calculation
Concentrate needs 48 tons/day, of which 60% is energy-based raw materials (mainly corn), about 28.8 tons, and 35% is protein-based raw materials, about 16.8 tons. Premix 5%, about 2.4 tons. Then the hourly output of ≥ 8 tons of concentrate can meet the requirements, 112 tons of roughage per day / day, of which 40% silage, about 44.8 tons, 67.2 tons of hay, hay is divided into wheat straw, corn straw, etc.
四、Process Design Analysis
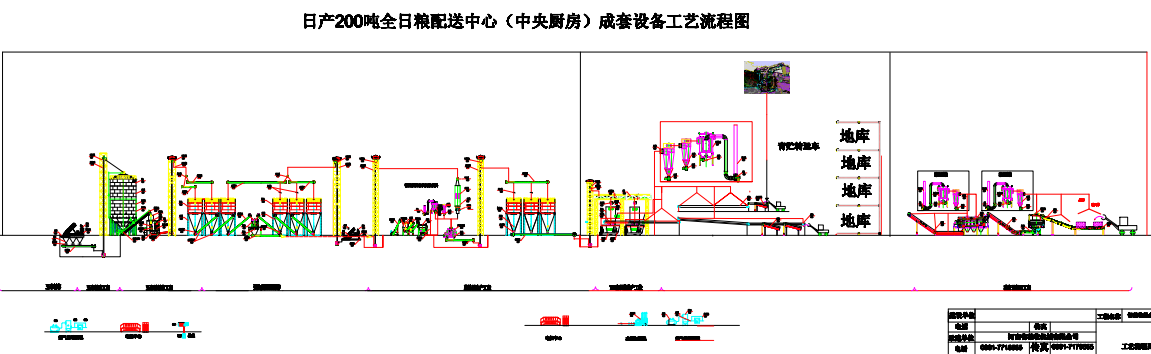
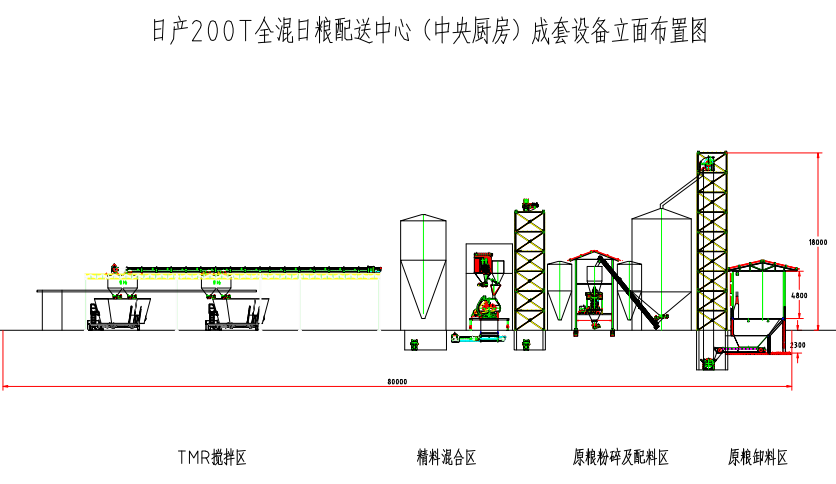
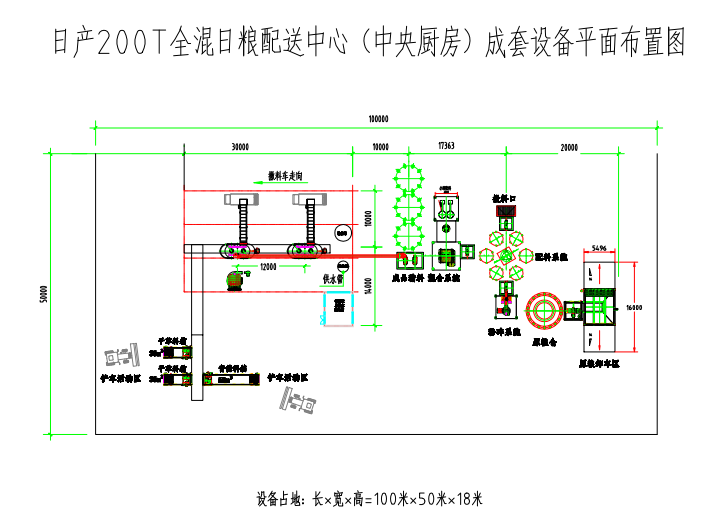
1、Steel plate silo and silo attachment system
Corn enters the steel plate silo for temporary storage by scraper and bucket lift through the grain unloading pit, which can bear the load of 30T truck, with overall dust removal system (pulse dust collector, fan) on it, and the steel plate silo is equipped with automatic temperature measurement system and ventilation system. It is equipped with the temporary storage capacity of 200 tons of energy grains (corn) for 7 days, which requires 28.8 tons of corn for daily grain and 200 tons for 7 days.
The angle of silo roof is 30°, the angle of cone bottom discharge is 45, the silo roof is equipped with natural ventilation window, manhole, guardrail and climbing ladder; the silo barrel is equipped with internal and external climbing ladder, silo door, platform and guardrail; the silo roof plate, enclosure plate and cone bottom plate are made of high quality hot-dip galvanized plate, the galvanized amount is 275g/m2; the column leg, ring beam and tension bar are hot-dip galvanized after processing
2、Corn crushing and corn meal storage system
The corn crushing system is equipped with a SWFP60-55 (55KW) crusher with an hourly output of 10 tons/hour. The crushing system is equipped with a pulse dust collector and the corn meal enters two corn meal storage bins through the elevator. Protein raw material enters the hopper through the feeding pit (with pulse dust collector on the feeding pit) and is conveyed by the hopper to 4 protein storage bins. The corn meal storage bins and protein storage bins are equipped with an outlet screw, which feeds different materials into the batching scale and feeds the matched materials into the mixing system through the scraper and elevator after finishing the batching.
The total capacity of the corn flour temporary storage bin is 57.6 tons to ensure the amount of cattle farm for 3 days, and two corn flour bins of 50m³ each (single bin: ø3.67m; 3.5 layers; height 8.04m; volume 50㎥) are hot-dip galvanized, the upper cone plate is 1.2mm thick; the lower cone plate is 1.5mm thick; the tower body plate is 1.0mm+1.0mm+1.0mm+1.2mm, and the column plate is 3.0mm thick; Galvanized layer thickness 275g/㎡; stainless steel material tower cover, 3mm hot-dip galvanized upper and lower flange, lower flange mouth diameter 440mm, height from the ground 900mm.
The bolts are M10 high strength Dacromet bolts.
3、Protein raw material temporary storage system
The silo body is hot-dip galvanized, the upper cone plate is 1.0mm thick; the lower cone plate is 1.2mm thick; the tower body plate is 1.0mm+1.0mm+1.2mm, the column plate is 2.5mm thick; the galvanized layer is 275g/㎡; the stainless steel tower cover, 3mm hot-dip galvanized upper and lower flange, the lower flange mouth diameter is 440mm, the height from the ground is 900mm. The bolts are M10 high strength Dacromet bolts.
Corn flour silo and protein raw material silo are 6 bins in total. 2 cubic meters of batching scales are set in the middle of the annular bin, 10-15 batches of batching per hour, batching volume ≥ 10 tons
4, premix temporary storage and mixing section of fine supplement, premix accounts for 5% of fine supplement, about 2.4 tons, purchased premix is stored temporarily in varieties, set up 2 temporary storage bins in the late fattening period, each 5 cubic bin, about 5 tons. Meet the needs of the cattle farm 2 days, bulk raw materials to be mixed bin 2, each 2 cubic meters, mixer volume 2 cubic meters, daily output ≥ 60 tons (1 * 10 * 6 = 60 tons)
5、Fine filler production section
Corn meal and protein raw materials enter the two buffer bins on the mixer through the batching scale, small materials enter the mixer through the stainless steel batching system and wind transport, the raw materials after mixing the batch of the mixer is the fine replenishment, the fine replenishment enters the 3 fine replenishment temporary storage bins through the bucket lift, each bin capacity is 44T, enough for 3 days of cattle farm production.
6、Whole-day food production section
Dairy farms need to use 160 tons of fully mixed rations per day, configured with two 30 cubic TMR machine (30 * 0.28 * 0.85 = 7 * 2 * 2 = 28 * 6 = 168 tons)
30 cubic TMR single production of lactating cows 7 tons of diet, diet CV value 10/2/2, uniformity ≧ 97%, cutter and shell of special design to ensure that the grain size of the diet is highly consistent, residual leftovers bottom < 5 kg, paddle < 30 kg, using the Italian "Comair" reducer, the United States "Avion" or "Digi star" weighing system, super wear-resistant steel (NM400) shell and stranded dragon service life > 30,000 hours, tons of daily grain energy consumption of 3.7 KW/h, NM400 steel shell, 25mm stranded dragon to increase the service life to 25mm stranded dragon makes the service life increased to 30,000-40,000 hours, reducing the cost of replacing the shell and stranded dragon when the equipment is in use for 3.5-4 years (14 hours/day), and the power consumption is 3.7-3.9 KW/h per ton of grain per day.
7、Straw pre-treatment system
Roughage is 112 tons/day, including 40% silage, about 44.8 tons, and 67.2 tons of hay, which is divided into wheat straw, corn straw, and alfalfa. The full mixed ration needs to add 18% water, about 60 tons of fiber raw materials need to be pretreated, set up 1 set of pretreatment system, capacity 10 tons / hour
The straw pre-treatment system is responsible for 70% of the raw material treatment in the full mixed diet, while the small volume of fiber raw materials, many types, complex impurities, easy to produce dust and other characteristics, is the bottleneck of the central kitchen to achieve intelligent operation, ruminant forage cost of fiber raw materials control is the most important element of competition in ruminant breeding enterprises
The whole system is divided into the untying and bale-breaking section - cleaning section - dust removal section - (crushing section)
(1) Bale breaking section: The bales of straw (small square bales, large square bales, second pressurized square bales, garden bales) are firstly put on the slatted chain conveyor platform by the grass grabber and conveyed to the untying mechanism through No.1 slatted chain conveyorl with frequency, where the tie ropes and nylon net ropes are cut out and the ropes are collected through the bypass.
The clipped rope bale loaded straw enters the bale breaker, which crushes the straw to 30-40 mm particle size and sends it to the next section by No.2 slat chain conveyor, the circuit is designed with frequency conversion motor.
(2) Sieving and cleaning section: The straw segments are transported to the sieving and cleaning section through the plate chain conveyor. Mainly there are straw cleaning sieve, fan, pulse dust collector, wind-closer, No.3 plate chain conveyor, permanent magnetic self-unloading iron remover and other equipment.
After crushing the straw segment, it is firstly passed through the permanent magnetic self-unloading iron remover to remove the iron-containing material after breaking the bale, which adopts a strong magnetic core composed of high-strength rare-earth NdFeB, with strong magnetic field and high magnetic field gradient, conveyor belt feeding iron removal, which can realize continuous iron absorption and abandonment, the belt has automatic deflection correction function, reliable operation and simple maintenance, and its internal magnetic circuit adopts perfect magnetic pole structure to guarantee the whole machine is trouble-free in harsh environment. Long-term operation, explosion-proof type, magnetic plate strength 150MT, cleaning 0.1-30 kg of ferromagnetic material, the
No.3 plate chain conveyor sends straw segments into straw cleaning sieve, cleaning sieve set up 4 different screen working surface, the materials entering the drum sieve take different trajectories through different specific gravity, and take the exit corresponding to the impractical screen through different shape size, which can clean up the dust, fine gravel in the straw. Auxiliary dust removal equipment system, can deal with the dust generated in the screening process. Fans, pulse dust collectors, wind closers to form an effective dust removal wind network.
(3) Dust removal system: No.1 plate chain conveyor is connected to the centralized dust removal wind network by installing sealed leather curtain above, the upper mouth of the broken bundle crusher has a dust removal cover connected to the centralized dust removal wind network, No.2 and No.3 plate chain conveyors are fully sealed with air outlets on the sealed cover every 2 meters connected to the dust removal wind network, and four dust removal ports are set on the cleaning sieve connected to the centralized dust removal wind network, the centralized dust removal system adopts fan-unloader-dust collector- The dust removal system adopts the combination of fan-unloader-dust collector-chimney to realize the dust-free workshop, the dust removal chimney is 15 meters high with spiral galvanized pipe, the motor has the function of explosion-proof, the alarm prompt function of fire hazard is set, and the indoor dust concentration is lower than 10mg/m3 and the outdoor dust concentration is lower than 150mg/m3.
(4) set 2 fiber raw material weighing bins, each volume 35 cubic meters, reduced weighing, box material: Q345. box material thickness bottom plate thickness ≥ 4mm side plate thickness ≥ 3mm
Power: 15Kw/each, box body 16Mn material, scraper chain conveyor mechanism heavy-duty conveyor chain. Set up a silage box, volume, 50m³ box material: 410 stainless steel external Q235 material frame, power: 30Kw / a, box body 410 stainless steel anti-corrosion material thickness ≥ 2.5mm, stainless steel anti-corrosion stirrer blade thickness > 4mm, the number of stirrer ≥ 2, scraper chain conveyor heavy-duty conveyor chain.
After pre-treatment, the clean segments enter the temporary storage bin, and then enter the TMR machine through the transfer belt machine after accurate weighing, and the silage raw material is put into the conveying bin after taking the material from the silage pick-up machine, and then enter the TMR machine through the transfer belt machine after weighing.
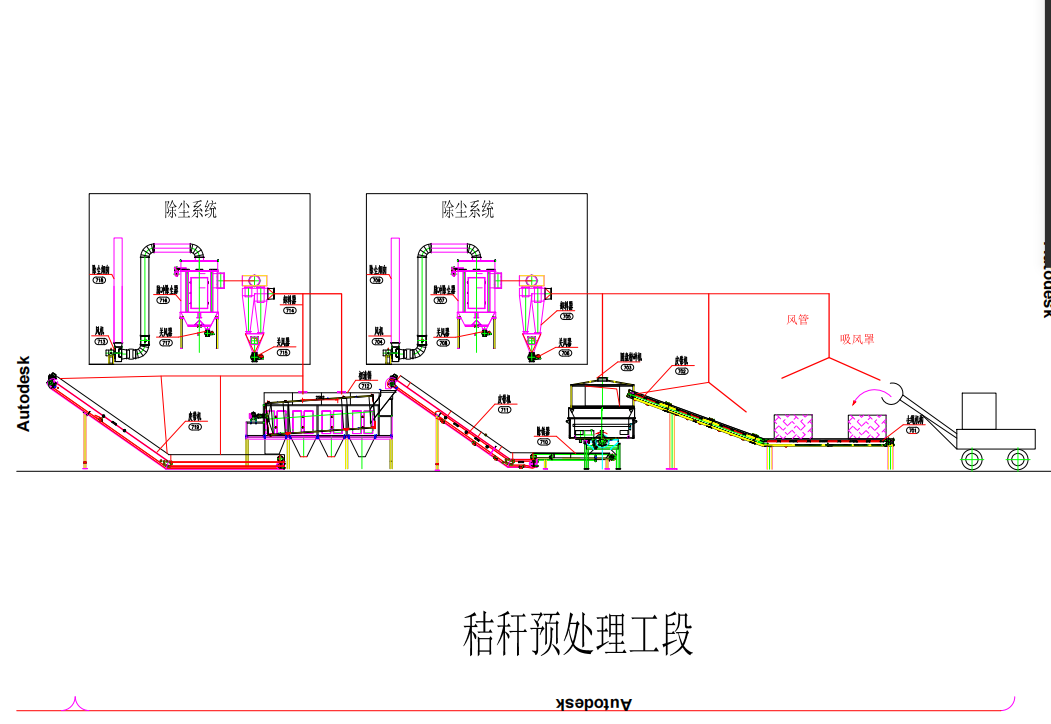
8、Auxiliary equipment.
(1) molasses pretreatment equipment: consists of liquid hot water heating storage tank, high and low level sensor, temperature sensor, stirring device, water pump, control valve, etc.
(2) Technical indicators
1、Liquid weighing and pressurizing spraying integrated equipment: capacity 80kg (water and honey);
2, single spraying time: 25-60 seconds / time (can be adjusted according to the amount of liquid);
3, spraying equipment: 4 spiral nozzle (can be used according to the amount of liquid to choose the number);
4, spraying liquid accuracy of about ± 0.5%, uniformity of about 90%.
Display operation function: On the main screen of the touch screen, the working status of the system process, process data and alarm information can be displayed in real time
Liquid replenishment function: liquid pretreatment equipment installed with level detection sensors, when the liquid is at a low limit, the system automatically sound and light alarm, while automatically open the honey pump to replenish the liquid, until the liquid reaches the set value to stop pumping honey
Quantitative honey spraying function: users can freely set the amount of honey spraying, the weight of the liquid, the time interval of honey spraying, the system according to the user's settings, automatic dosing, automatic honey spraying, record query, report function: automatic record, storage of temperature, spraying liquid volume and other data, with the function of query.
Delay function: the system equipment has spraying liquid time delay, atomization time delay, cleaning pipe delay, cleaning pipe time adjustable function. System with weighing start automatically clear zero, automatic replenishment function
Cleaning function: the use of compressed air to automatically blow the spray tank and the spray pipeline and nozzle; normal cleaning of the pipeline on a regular basis without blockage.
Protection function: with automatic pressurization, depressurization, intermittent liquid spraying, system self-protection and other functions, so that the motor, pump, valve and other electrical and pipeline in the best working condition to extend the service life of the equipment.
Easy to operate: control system operation is simple and easy to understand, man-machine dialogue, set the weight of the weight of the liquid to be added on the touch screen, the batch to be added can be put into production use without professional training
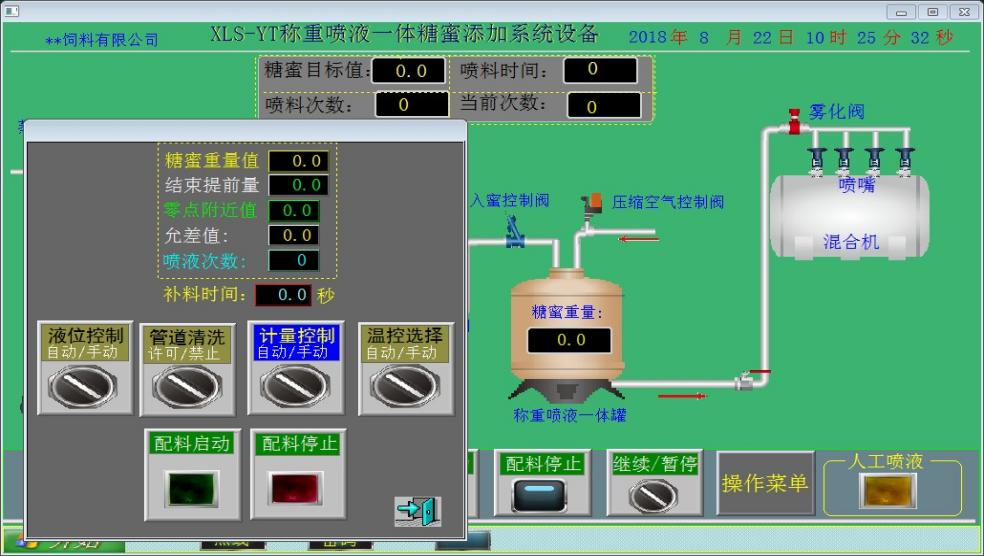
(3) Water adding system.
(including buffer tank, discharge pump, pipeline, water distributor, automatic valve) main pipeline to send water to the insulation water tank, with high liquid level control low liquid level protection, with variable frequency pump water, single TMR water addition speed of not less than 60T/min.
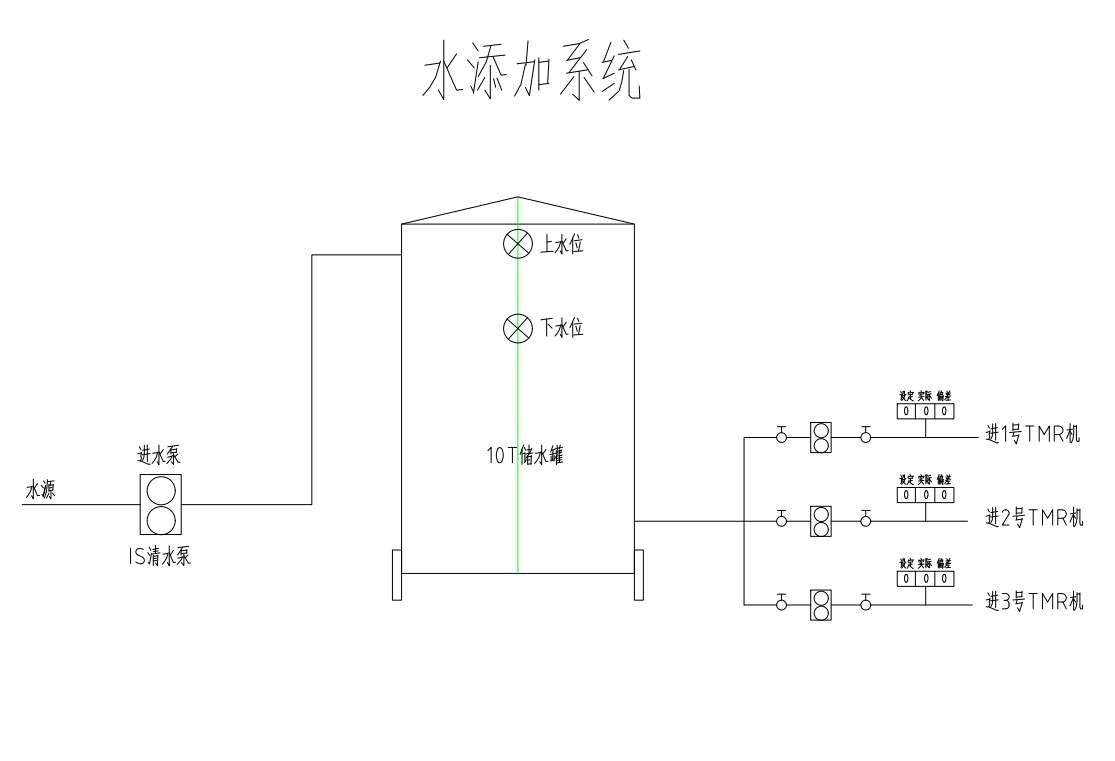
9、Centralized control and feeding management system
Select the U.S. DIGI-STAR precision feeding management system and centralized control system, the system is now widely used in large domestic ranches fixed feeding station; the system is configured with reliable hardware and software quality, good quality, stable performance, is currently the first-line brand preferred by large domestic ranches.
The program uses functional modular design program, is based on PLC and SCADS (SupervioryCtontrol And Data Acquisition / data acquisition and monitoring) intelligent control system, and realize the internal information of the ranch seamlessly. The functional modules are: TMR Tracker precise feeding software module, which realizes feeding recipe making, feeding data sending and receiving, and processing of table reports; TMR diet making module, which realizes material adding, multi-speed TMR mixing control, diet feeding; roughage processing module, which realizes roughage adding according to recipe requirements; data transmission module, which realizes automatic data transfer between diet making system and concentrate system. The data transmission module realizes automatic data transmission and processing of the diet making system and concentrate system, and data docking with third-party software, etc.
Centralized control and feeding management system
Design scheme.
Centralized control system as the core of the whole feeding station system, centralized data processing and task allocation. The coarse feed addition prompt, concentrate feed automatic control system and precise feeding management system are integrated by the industrial control system for the control part and operated in the same control platform. The control process is as follows.
(1) TMR diet production: TMR Tracker precision feeding software is responsible for the production of formulas and sends the formulas of different sections to different control systems through network or wireless, and carries out information collection of various diets made by itself and generates various data reports, which include various reports on the accuracy of diet production, accuracy of spreading personnel operation, feeding situation, dry matter intake, raw material consumption, etc. The reports can be exported upon request.
(2) Concentrate feed production and addition: The concentrate PLC control system collects the concentrate formula data from the precise feeding system TMR Tracker feeding management software and realizes direct data transmission. The concentrate PLC system makes concentrate and delivers it to the corresponding position according to the formula requirements and automatically controls the process of concentrate addition.
(3) Coarse feed conveyor adding: precise feeding system TMR Tracker feeding management software coarse feed formula data, feeding system for each coarse feed formula data processing display in each mixer truck display on the big screen, prompting the forklift driver to add to the corresponding TMR preparation machine in accordance with the order of adding, weight in turn.
10、System safety design scheme
(1). Dust and explosion-proof safety control measures in the workshop
The full mixed ration production line is the integration of different segments such as silage, fiber raw materials and fine supplement production, with centralized management and monitoring of equipment. There are important dust and explosion control areas including fiber raw material pre-treatment, fiber raw material storage and transportation, etc. Dust control and explosion control are particularly important to ensure the safe operation of the complete system. This section as the primary content of the whole-day food distribution center set targeted prevention system. The key links of feeding and discharging ports adopt the combination of fan-unloader-dust collector-chimney to achieve a dust-free workshop, and the motor is equipped with explosion-proof function, and the alarm amount of fire hazard is set to prompt the function.
(2). Three waste management
According to the production characteristics of the workshop, the workshop production process does not produce exhaust gas, wastewater, but there are dust and noise hazards, in order to ensure the health of workers and the surrounding environment is not polluted, the design according to the relevant national norms, take a single machine dust, set up more dust removal network, isolate the main noise sources, to be integrated management.
Noise treatment of this workshop is the main source of noise is the crusher, fan, compressor, granular raw materials and the collision of the wall noise, the design uses the following measures to ensure that the noise ≤ 85dB (A), crusher, fan configuration silencer, crusher set isolation room, crusher soft start.
Dust treatment
①In the raw material feeding mouth are equipped with suction dust collector, dust chimney {15 meters high spiral galvanized pipe)
②The whole system in the operation process to ensure that it works under negative pressure as far as possible, that is, where a single machine can be set up suction dust removal, the use of a single machine suction dust removal, other parts are equipped with dust-absorbing air network, dust-containing air before discharge are filtered through the pulse bag filter to ensure that the indoor dust concentration is less than 10mg/m3 , outdoor dust concentration is less than 150mg/m3 ;
③Strengthen the sealing performance of the equipment
(3). Labor protection
①The dust source is mainly sealed, supplemented by dust removal measures to effectively reduce the concentration of dust in the warehouse, below the explosion point
②In the staff operation and maintenance parts, are set up platform, railings, warning signs
③Electrostatic grounding to prevent sparks
④ high degree of automation, greatly improve the operating conditions of production workers, reduce the labor intensity of workers
Summary.
The choice of "central kitchen" forage production mode ensures the advanced, practical, reliable and economic forage processing project, occupies the high point in the regional industry and has the value of promotion and demonstration in the region, the program operates in a system program, commanding the whole process through computer or touch screen in the central control room, no one is on site, realizing accurate Weighing, precise feeding, data collection and analysis, guiding production, providing a wise solution for the realization of digital breeding of forage plate
11. Complete set of equipment operation guarantee system
Henan Province Hengmu Machinery Co., Ltd. always takes "turning the enterprise into a school and building a professional feed machinery training and trusteeship team in China" as its goal to pursue. In order to ensure that users can give full play to the advanced economic production performance of complete sets of equipment and minimize production costs.
First of all, the "central kitchen" system to develop a training program: sub-management procedures, operating procedures, maintenance and maintenance procedures, general equipment troubleshooting procedures, equipment intact in the medium and long-term assessment standards, the organization of operators and managers training examinations, the examination of those who pass the issuance of the certificate of induction operations
I. Division regulations, each section, each post clear operators, managers, job responsibilities include: daily inspection content and regular inspection content, daily inspection content will be developed according to the characteristics of the equipment inspection content, such as the crusher time point bearing temperature rise, crusher noise, crushing raw materials crushing rate, etc.
II. Operating procedures: including safety procedures, pre-start inspection, start-up sequence, shutdown, shutdown sequence, check after shutdown and other content.
Three. Maintenance and repair procedures: in accordance with the overall goal of heavy maintenance, light maintenance, to achieve priority planned downtime, for different equipment characteristics of their own detailed maintenance and maintenance plans, each equipment maintenance time, grease type, maintenance responsibility, maintenance supervision, the normal maintenance process diagram.
IV. Equipment troubleshooting knowledge and contingency plans: a catalog of possible failures and corresponding solutions for each equipment, emergency plans in case of problems that cannot be solved in one hour, including control system bypass conversion, timely availability of spare machines. Accessories set alarm line, etc.
V. Assessment of equipment intact status in the medium and long term.
1. According to industry norms and equipment configuration of the complete system. The years of equipment use, determine the regular time and evaluation criteria, to determine whether the equipment enters the limit of technical state, mainly in accordance with the technical principles of whether it can continue to work; should not continue to work the operating safety principles and appropriate not suitable to continue to work, due to the sharp increase in the degree of wear and tear of the equipment, and the equipment failure rate increases, resulting in excessive downtime, can not work properly or work time can not guarantee.
2、The method of technical and economic analysis is used to determine
Production capacity weakened significantly, energy consumption is too large, the input-output ratio is seriously unreasonable and uneconomic. Such as crushed products, granulation products, low electricity production; unit hourly production capacity is much lower than the design hourly output.
3, the main quality indicators of machinery and equipment to determine the degree of deterioration
The quality of the work of the equipment itself and the quality of product production deterioration is obvious, such as crusher vibration is too large, crushing particle size is not uniform; mixer residue is too large, mixing uniformity coefficient of variation is too large.
The above three situations, as long as one of them can be considered that the equipment has reached the limit of damage.
VI. Establishment of the central kitchen equipment files
The file consists of equipment ledger, single machine equipment file, general parts file, parts inventory plan, parts inventory records, ring mold file, etc. Equipment ledger one page per piece of equipment, summarized in a book.
1、Equipment ledger
First established by the engineering department, two copies, one of which should be transferred to the branch production department when the new plant or the old plant after leasing transformation, the other one is kept by the engineering department; branch production department to receive the equipment ledger and the workshop equipment and peripheral equipment for comparison, be sure that the accuracy of the file to keep; after the equipment is put into operation, such as technical changes or replacement of equipment, the equipment ledger should be made correction.
The equipment ledger of each branch is kept in the office of the production department.
2、Single machine equipment file
The production department receives the car
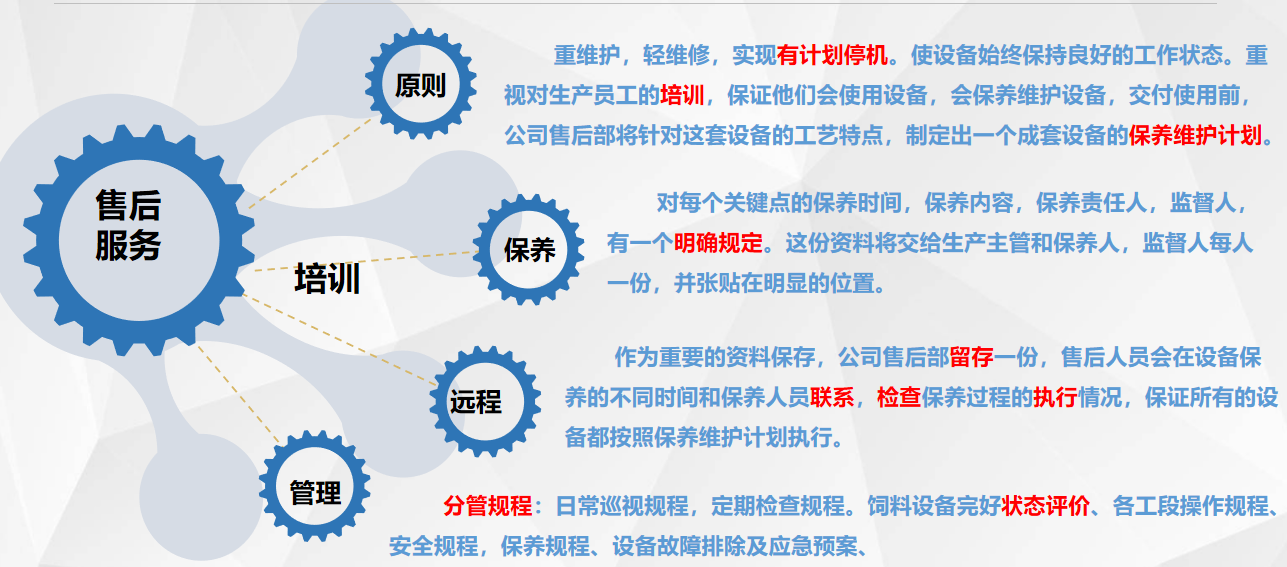
Henan Province Hengmu Machinery Co.
Address: Shihe Road, Xiwu County, Henan Province, Industrial Cluster Area
Tel: 0391-7715555 0391-7179555
Website: www.jiemujixie.com
March 21, 2022
Finished pellets
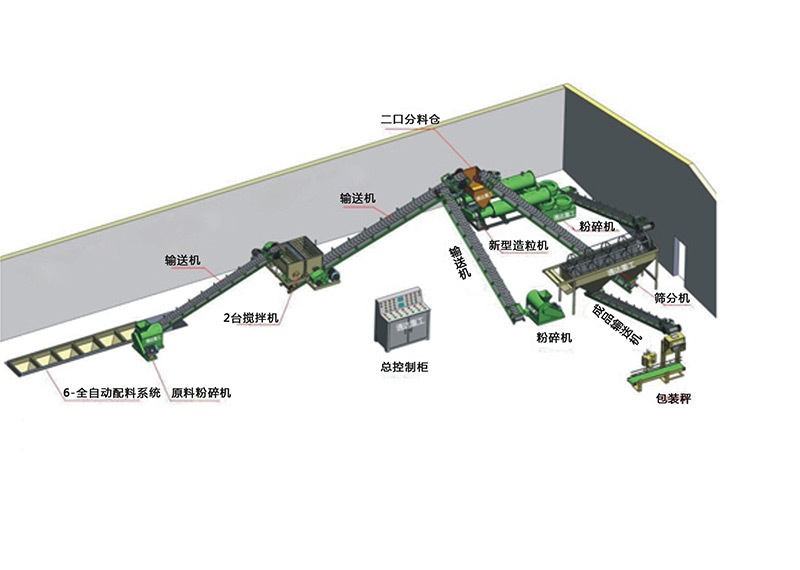
Organic fertilizer production line

Slag name
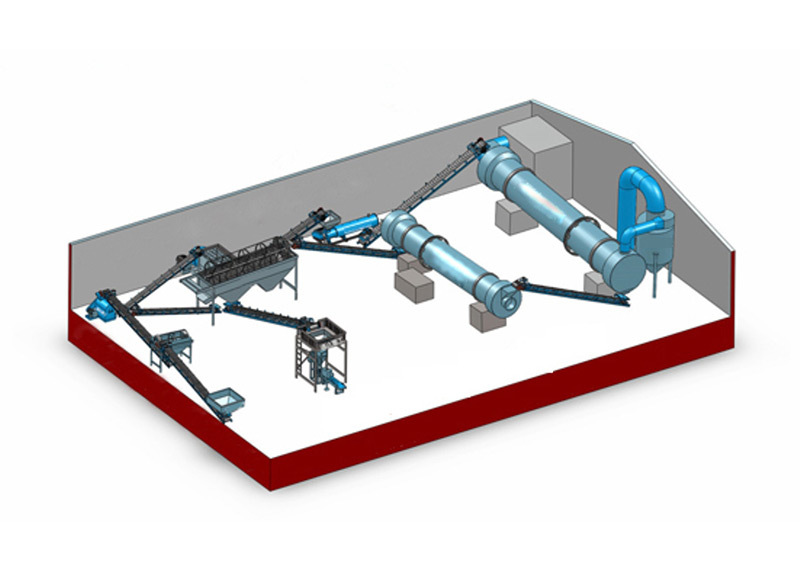
Organic fertilizer and detailed text
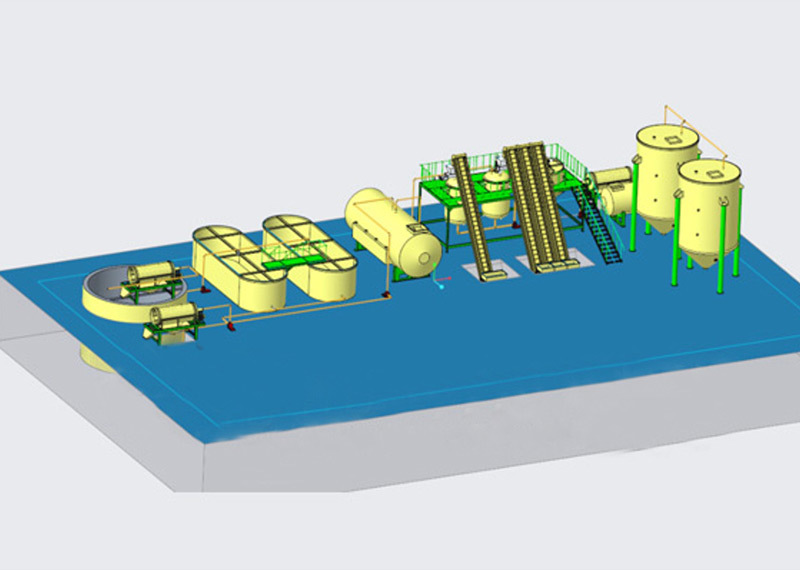
Water soluble fertilizer
Related Equipment
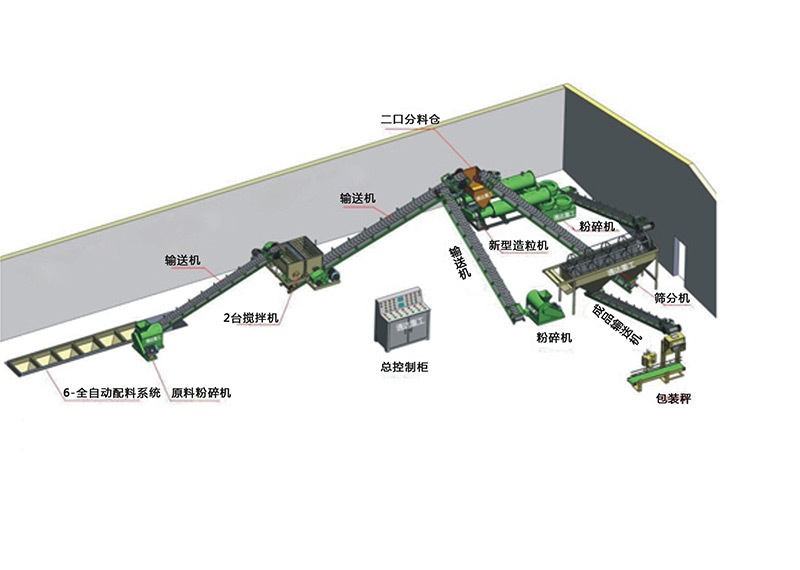
Organic fertilizer production line

Slag name
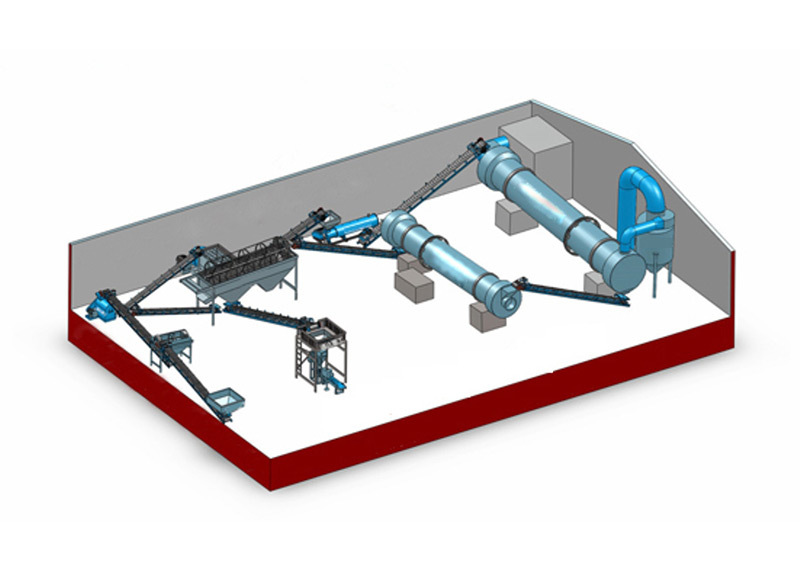
Organic fertilizer and detailed text
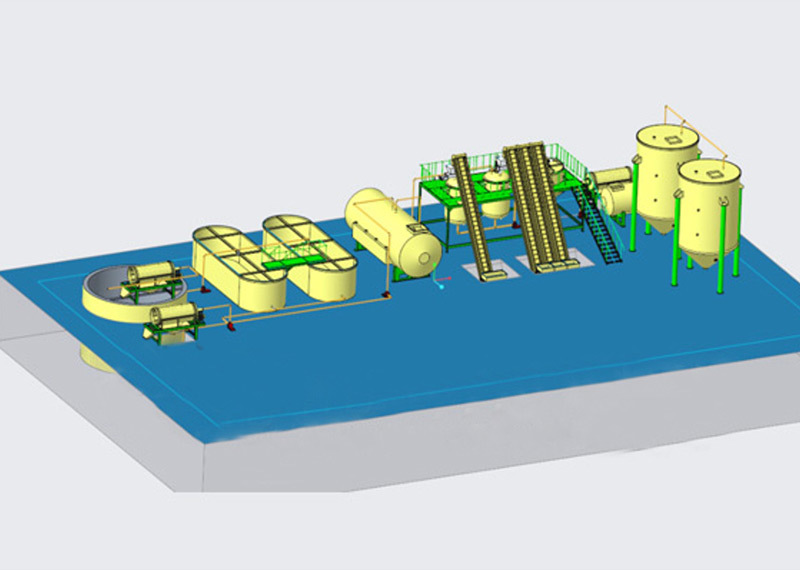
Water soluble fertilizer
Online Inquiry