Dust and explosion-proof safety control equipment
- Production capacity: 10-30 cubic meters/h
- Applicable materials: Silage raw materials, fiber raw materials, fine feed production, etc.
- Applications: Raw material pretreatment, temporary storage and transportation of raw materials, etc.
Classification:
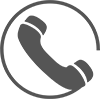
Tel:
Introduction
-
(1) Workshop dust and explosion-proof safety control measures
The total mixed ration production line is the integration of different sectors such as silage raw materials, fiber raw materials, and concentrated feed production. The equipment is centrally managed and monitored.
Among them, there are important prevention and control areas for dust removal and explosion protection, including fiber raw material pretreatment, temporary storage and transportation of fiber raw materials, etc., dust control and explosion protection control
It is particularly important to ensure the safe operation of the complete system. As the primary content of the whole ration distribution center, this section sets up a targeted prevention system.
The feeding port and the discharging port of the key link adopt the combination of fan-unloader-dust collector-chimney to achieve no dust in the workshop, and the motor has explosion-proof function.
Set the alarm amount reminder function of fire insurance.
(2) Three-waste management
According to the production characteristics of the production workshop, no waste gas and waste water are produced in the production process of the workshop, but there are hazards of dust and noise. In order to ensure the safety of workers
The body health and the surrounding environment are not polluted. The design is in accordance with the relevant national standards, using a single machine to remove dust, setting up multiple dust removal outlets, isolating the main noise sources, and comprehensively treating them. Noise control The main source of noise in this workshop is the noise generated by the crusher, fan, compressor, and the collision of granular raw materials with the pipe wall. The design adopts the following measures to ensure that the noise is less than or equal to 85dB(A). The crusher and fan are equipped with mufflers and crushers. Set up an isolation room, and the crusher starts softly.
Dust treatment
①A suction dust collector and a dust removal chimney (15m high spiral galvanized pipe) are equipped at the raw material feeding port.
② The whole system should work under negative pressure as much as possible during the operation process, that is, where a single machine can be installed for suction and dust removal, single machine suction and dust removal are used. Filtered by a pulse bag filter to ensure that the indoor dust concentration is lower than 10mg/m3 and the outdoor dust concentration is lower than 150mg/m3;
③Strengthen the sealing performance of the equipment
(3) Labor protection
① The dust source is mainly sealed and the dust removal is supplemented, which can effectively reduce the dust concentration in the warehouse, which is lower than the explosion point.
②In the parts operated and maintained by the staff, platforms, railings and warning signs are set up
③Electrostatic grounding to prevent sparks
④The high degree of automation greatly improves the operating conditions of production workers and reduces the labor intensity of workers
-
-
As the primary content of the whole ration distribution center, set up a targeted prevention system.
The feeding port and the discharging port of the key link adopt the combination of fan-unloader-dust collector-chimney to achieve no dust in the workshop, and the motor has explosion-proof function.
Set the alarm amount reminder function of fire insurance。
-
For more product details: please call 15993745555
Finished pellets
undefined
Features
-
- Commodity name: Dust and explosion-proof safety control equipment
- Production capacity: 10-30 cubic meters/h
- Applicable materials: Silage raw materials, fiber raw materials, fine feed production, etc.
- Applications: Raw material pretreatment, temporary storage and transportation of raw materials, etc.
(1) Workshop dust and explosion-proof safety control measures
The total mixed ration production line is the integration of different sectors such as silage raw materials, fiber raw materials, and concentrated feed production. The equipment is centrally managed and monitored.
Among them, there are important prevention and control areas for dust removal and explosion protection, including fiber raw material pretreatment, temporary storage and transportation of fiber raw materials, etc., dust control and explosion protection control
It is particularly important to ensure the safe operation of the complete system. As the primary content of the whole ration distribution center, this section sets up a targeted prevention system.
The feeding port and the discharging port of the key link adopt the combination of fan-unloader-dust collector-chimney to achieve no dust in the workshop, and the motor has explosion-proof function.
Set the alarm amount reminder function of fire insurance.
(2) Three-waste management
According to the production characteristics of the production workshop, no waste gas and waste water are produced in the production process of the workshop, but there are hazards of dust and noise. In order to ensure the safety of workers
The body health and the surrounding environment are not polluted. The design is in accordance with the relevant national standards, using a single machine to remove dust, setting up multiple dust removal outlets, isolating the main noise sources, and comprehensively treating them. Noise control The main source of noise in this workshop is the noise generated by the crusher, fan, compressor, and the collision of granular raw materials with the pipe wall. The design adopts the following measures to ensure that the noise is less than or equal to 85dB(A). The crusher and fan are equipped with mufflers and crushers. Set up an isolation room, and the crusher starts softly.
Dust treatment
①A suction dust collector and a dust removal chimney (15m high spiral galvanized pipe) are equipped at the raw material feeding port.
② The whole system should work under negative pressure as much as possible during the operation process, that is, where a single machine can be installed for suction and dust removal, single machine suction and dust removal are used. Filtered by a pulse bag filter to ensure that the indoor dust concentration is lower than 10mg/m3 and the outdoor dust concentration is lower than 150mg/m3;
③Strengthen the sealing performance of the equipment
(3) Labor protection
① The dust source is mainly sealed and the dust removal is supplemented, which can effectively reduce the dust concentration in the warehouse, which is lower than the explosion point.
②In the parts operated and maintained by the staff, platforms, railings and warning signs are set up
③Electrostatic grounding to prevent sparks
④The high degree of automation greatly improves the operating conditions of production workers and reduces the labor intensity of workers
-
-
As the primary content of the whole ration distribution center, set up a targeted prevention system.
The feeding port and the discharging port of the key link adopt the combination of fan-unloader-dust collector-chimney to achieve no dust in the workshop, and the motor has explosion-proof function.
Set the alarm amount reminder function of fire insurance。
-
For more product details: please call 15993745555
Working Principle
-
- Commodity name: Dust and explosion-proof safety control equipment
- Production capacity: 10-30 cubic meters/h
- Applicable materials: Silage raw materials, fiber raw materials, fine feed production, etc.
- Applications: Raw material pretreatment, temporary storage and transportation of raw materials, etc.
(1) Workshop dust and explosion-proof safety control measures
The total mixed ration production line is the integration of different sectors such as silage raw materials, fiber raw materials, and concentrated feed production. The equipment is centrally managed and monitored.
Among them, there are important prevention and control areas for dust removal and explosion protection, including fiber raw material pretreatment, temporary storage and transportation of fiber raw materials, etc., dust control and explosion protection control
It is particularly important to ensure the safe operation of the complete system. As the primary content of the whole ration distribution center, this section sets up a targeted prevention system.
The feeding port and the discharging port of the key link adopt the combination of fan-unloader-dust collector-chimney to achieve no dust in the workshop, and the motor has explosion-proof function.
Set the alarm amount reminder function of fire insurance.
(2) Three-waste management
According to the production characteristics of the production workshop, no waste gas and waste water are produced in the production process of the workshop, but there are hazards of dust and noise. In order to ensure the safety of workers
The body health and the surrounding environment are not polluted. The design is in accordance with the relevant national standards, using a single machine to remove dust, setting up multiple dust removal outlets, isolating the main noise sources, and comprehensively treating them. Noise control The main source of noise in this workshop is the noise generated by the crusher, fan, compressor, and the collision of granular raw materials with the pipe wall. The design adopts the following measures to ensure that the noise is less than or equal to 85dB(A). The crusher and fan are equipped with mufflers and crushers. Set up an isolation room, and the crusher starts softly.
Dust treatment
①A suction dust collector and a dust removal chimney (15m high spiral galvanized pipe) are equipped at the raw material feeding port.
② The whole system should work under negative pressure as much as possible during the operation process, that is, where a single machine can be installed for suction and dust removal, single machine suction and dust removal are used. Filtered by a pulse bag filter to ensure that the indoor dust concentration is lower than 10mg/m3 and the outdoor dust concentration is lower than 150mg/m3;
③Strengthen the sealing performance of the equipment
(3) Labor protection
① The dust source is mainly sealed and the dust removal is supplemented, which can effectively reduce the dust concentration in the warehouse, which is lower than the explosion point.
②In the parts operated and maintained by the staff, platforms, railings and warning signs are set up
③Electrostatic grounding to prevent sparks
④The high degree of automation greatly improves the operating conditions of production workers and reduces the labor intensity of workers
-
-
As the primary content of the whole ration distribution center, set up a targeted prevention system.
The feeding port and the discharging port of the key link adopt the combination of fan-unloader-dust collector-chimney to achieve no dust in the workshop, and the motor has explosion-proof function.
Set the alarm amount reminder function of fire insurance。
-
For more product details: please call 15993745555
Technical parameters
-
- Commodity name: Dust and explosion-proof safety control equipment
- Production capacity: 10-30 cubic meters/h
- Applicable materials: Silage raw materials, fiber raw materials, fine feed production, etc.
- Applications: Raw material pretreatment, temporary storage and transportation of raw materials, etc.
(1) Workshop dust and explosion-proof safety control measures
The total mixed ration production line is the integration of different sectors such as silage raw materials, fiber raw materials, and concentrated feed production. The equipment is centrally managed and monitored.
Among them, there are important prevention and control areas for dust removal and explosion protection, including fiber raw material pretreatment, temporary storage and transportation of fiber raw materials, etc., dust control and explosion protection control
It is particularly important to ensure the safe operation of the complete system. As the primary content of the whole ration distribution center, this section sets up a targeted prevention system.
The feeding port and the discharging port of the key link adopt the combination of fan-unloader-dust collector-chimney to achieve no dust in the workshop, and the motor has explosion-proof function.
Set the alarm amount reminder function of fire insurance.
(2) Three-waste management
According to the production characteristics of the production workshop, no waste gas and waste water are produced in the production process of the workshop, but there are hazards of dust and noise. In order to ensure the safety of workers
The body health and the surrounding environment are not polluted. The design is in accordance with the relevant national standards, using a single machine to remove dust, setting up multiple dust removal outlets, isolating the main noise sources, and comprehensively treating them. Noise control The main source of noise in this workshop is the noise generated by the crusher, fan, compressor, and the collision of granular raw materials with the pipe wall. The design adopts the following measures to ensure that the noise is less than or equal to 85dB(A). The crusher and fan are equipped with mufflers and crushers. Set up an isolation room, and the crusher starts softly.
Dust treatment
①A suction dust collector and a dust removal chimney (15m high spiral galvanized pipe) are equipped at the raw material feeding port.
② The whole system should work under negative pressure as much as possible during the operation process, that is, where a single machine can be installed for suction and dust removal, single machine suction and dust removal are used. Filtered by a pulse bag filter to ensure that the indoor dust concentration is lower than 10mg/m3 and the outdoor dust concentration is lower than 150mg/m3;
③Strengthen the sealing performance of the equipment
(3) Labor protection
① The dust source is mainly sealed and the dust removal is supplemented, which can effectively reduce the dust concentration in the warehouse, which is lower than the explosion point.
②In the parts operated and maintained by the staff, platforms, railings and warning signs are set up
③Electrostatic grounding to prevent sparks
④The high degree of automation greatly improves the operating conditions of production workers and reduces the labor intensity of workers
-
-
As the primary content of the whole ration distribution center, set up a targeted prevention system.
The feeding port and the discharging port of the key link adopt the combination of fan-unloader-dust collector-chimney to achieve no dust in the workshop, and the motor has explosion-proof function.
Set the alarm amount reminder function of fire insurance。
-
For more product details: please call 15993745555
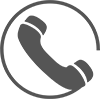
Tel:
Related Equipment
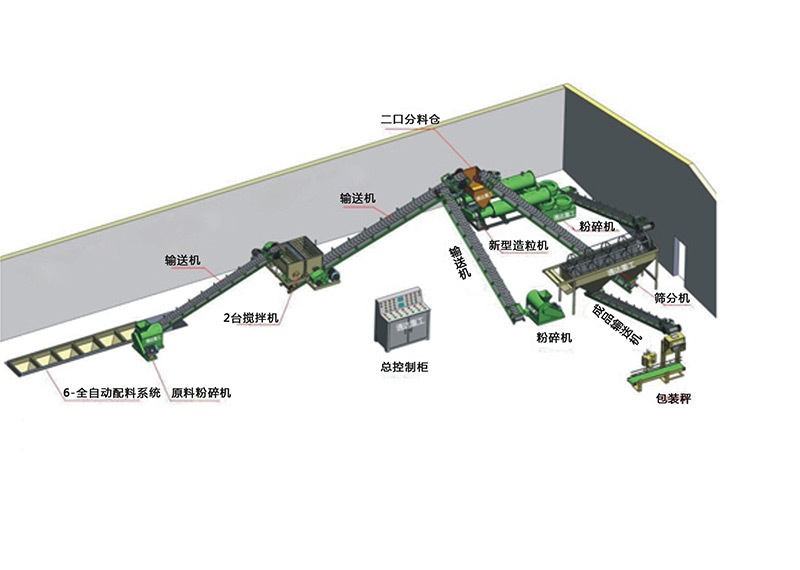
Organic fertilizer production line

Slag name
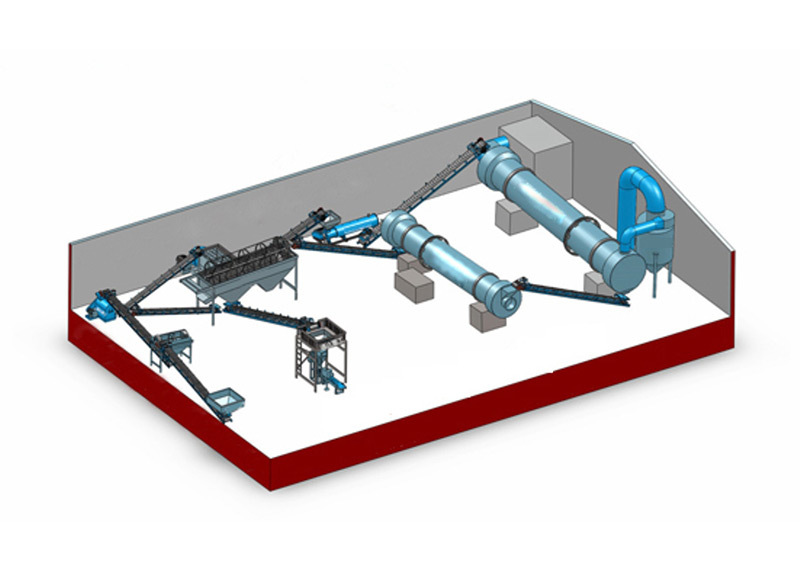
Organic fertilizer and detailed text
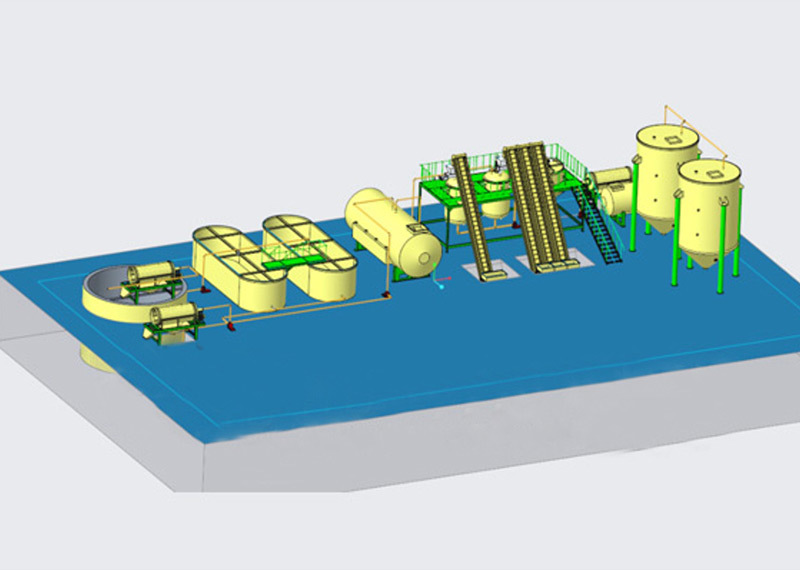
Water soluble fertilizer
Inquiry