Straw Pretreatment System
- Production capacity: 5-20t/h
- Applicable materials: feed fiber, etc.
- Applications: pasture, etc.
Classification:
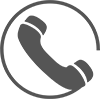
Tel:
Introduction
-
The straw pretreatment system undertakes 70% of the raw material processing tasks in the total mixed ration. Due to the small volume, large volume, many types of fibrous raw materials, complex impurities, and easy generation of dust, the supercritical value of dust concentration has the characteristics of the danger of electrostatic explosion, etc. , is the bottleneck for the realization of intelligent operation in the central kitchen of the pasture. In the cost of ruminant forage, the cost control of fiber raw materials is an important element of competition among ruminant breeding enterprises.
The whole system is divided into rope unwinding section - bundling section - cleaning section - dust removal section - (crushing section)
(1) Unpacking machine: The unpacking machine realizes the separation of the foreskin and the straw bale through continuous actions such as cutting the foreskin - hooking the foreskin - collecting the foreskin.
(2) Bale breaking section: baling straw (small square bales, large square bales, secondary pressure square bales, garden bales), first put the straw bales on the plate chain conveyor platform through the grass grabber, and pass the No. 1 plate The chain conveyor 1 is frequency-converted and conveyed to the unroping mechanism, and the tie rope and nylon net rope are cut out, and the rope is collected through the bypass.
The bundled straw with the rope cut off enters the baler breaker. The baler breaks the straw to a particle size of 30-40 mm, and is sent to the next section by the No. 2 plate chain conveyor. The circuit design adopts a frequency conversion motor.
Screening and cleaning section: The straw segment is transported to the screening and cleaning section through the plate chain conveyor. There are mainly straw cleaning screens, fans, pulse dust collectors, air locks, No. 3 plate chain conveyors, permanent magnet self-unloading type dust collectors Iron and other equipment.
(3) After the broken straw segment is broken, the iron-containing material is first removed by a permanent magnet self-unloading iron remover, and high-strength rare earth NdFeB is used to form a strong magnetic core, which has a strong magnetic field and a high magnetic field gradient, and the conveyor belt conveys The material and iron removal can realize continuous iron absorption and abandonment. The belt has automatic deviation correction function, reliable operation and simple maintenance. Its internal magnetic circuit adopts a perfect magnetic pole structure to ensure that the whole machine can operate without failure for a long time in harsh environments. Explosion-proof type, Magnetic plate strength 150MT, cleaning 0.1-30 kg of ferromagnetic material,
The No. 3 plate chain conveyor sends the straw segments into the straw cleaning screen. There are 4 different screen mesh working surfaces in the cleaning screen. The materials entering the trommel screen follow different trajectories through different specific gravity, and cannot pass through the screen due to different external dimensions. The corresponding outlet can clean up the dust and fine gravel in the straw. Auxiliary dust removal equipment system can handle the dust generated during the screening process. Fans, pulse dust collectors and air closers form an effective dust removal air network.
(4) Dust removal system: the top of the No. 1 chain conveyor is connected to the centralized dust removal air net by installing a sealing leather curtain.
The number plate chain conveyor is fully sealed, the air outlet on the sealing cover is connected to the dust removal air net every 2 meters, and 4 dust removal ports are set on the cleaning screen to connect with the centralized dust removal air network. The centralized dust removal system adopts the fan-discharger-dust collector. -The combination of chimneys can achieve no dust in the workshop, and the 15-meter-high spiral galvanized pipe of the dust-removing chimney, the motor has explosion-proof function, and the alarm function of fire danger is set, so that the indoor dust concentration is lower than 10mg/m3, and the outdoor dust concentration is lower than 150mg/ m3.
(5) Set up a number of fiber raw material weighing bins, each with a volume of 35 cubic meters, weight reduction, and box material: Q345. Box material thickness Bottom plate thickness ≥ 4mm Side plate thickness ≥ 3mm
Power: 15Kw/piece, box body 16Mn material, scraper chain conveyor mechanism heavy-duty conveyor chain. Set up multiple silage bins, the volume is 50m3, the box material is 304 stainless steel, the external Q235 material frame, power: 30Kw/piece, the thickness of the 304 stainless steel anti-corrosion material of the box body is ≥ 2.5mm, the thickness of the stainless steel anti-corrosion auger blade> 4mm, the stirring The number of dragons is ≥2, and the scraper chain conveyor mechanism is heavy-duty conveyor chain.
After pretreatment, the clean segment enters the weighing bin, and after being accurately weighed, it enters the TMR machine through the transfer belt conveyor.
Enter the TMR machine through the transfer belt conveyor.
-
The whole system is divided into rope unwinding section - bundling section - cleaning section - dust removal section - (crushing section)
-
For more product details: please call 15993745555
Finished pellets
undefined
Features
-
- Commodity name: Straw Pretreatment System
- Production capacity: 5-20t/h
- Applicable materials: feed fiber, etc.
- Applications: pasture, etc.
The straw pretreatment system undertakes 70% of the raw material processing tasks in the total mixed ration. Due to the small volume, large volume, many types of fibrous raw materials, complex impurities, and easy generation of dust, the supercritical value of dust concentration has the characteristics of the danger of electrostatic explosion, etc. , is the bottleneck for the realization of intelligent operation in the central kitchen of the pasture. In the cost of ruminant forage, the cost control of fiber raw materials is an important element of competition among ruminant breeding enterprises.
The whole system is divided into rope unwinding section - bundling section - cleaning section - dust removal section - (crushing section)
(1) Unpacking machine: The unpacking machine realizes the separation of the foreskin and the straw bale through continuous actions such as cutting the foreskin - hooking the foreskin - collecting the foreskin.
(2) Bale breaking section: baling straw (small square bales, large square bales, secondary pressure square bales, garden bales), first put the straw bales on the plate chain conveyor platform through the grass grabber, and pass the No. 1 plate The chain conveyor 1 is frequency-converted and conveyed to the unroping mechanism, and the tie rope and nylon net rope are cut out, and the rope is collected through the bypass.
The bundled straw with the rope cut off enters the baler breaker. The baler breaks the straw to a particle size of 30-40 mm, and is sent to the next section by the No. 2 plate chain conveyor. The circuit design adopts a frequency conversion motor.
Screening and cleaning section: The straw segment is transported to the screening and cleaning section through the plate chain conveyor. There are mainly straw cleaning screens, fans, pulse dust collectors, air locks, No. 3 plate chain conveyors, permanent magnet self-unloading type dust collectors Iron and other equipment.
(3) After the broken straw segment is broken, the iron-containing material is first removed by a permanent magnet self-unloading iron remover, and high-strength rare earth NdFeB is used to form a strong magnetic core, which has a strong magnetic field and a high magnetic field gradient, and the conveyor belt conveys The material and iron removal can realize continuous iron absorption and abandonment. The belt has automatic deviation correction function, reliable operation and simple maintenance. Its internal magnetic circuit adopts a perfect magnetic pole structure to ensure that the whole machine can operate without failure for a long time in harsh environments. Explosion-proof type, Magnetic plate strength 150MT, cleaning 0.1-30 kg of ferromagnetic material,
The No. 3 plate chain conveyor sends the straw segments into the straw cleaning screen. There are 4 different screen mesh working surfaces in the cleaning screen. The materials entering the trommel screen follow different trajectories through different specific gravity, and cannot pass through the screen due to different external dimensions. The corresponding outlet can clean up the dust and fine gravel in the straw. Auxiliary dust removal equipment system can handle the dust generated during the screening process. Fans, pulse dust collectors and air closers form an effective dust removal air network.
(4) Dust removal system: the top of the No. 1 chain conveyor is connected to the centralized dust removal air net by installing a sealing leather curtain.
The number plate chain conveyor is fully sealed, the air outlet on the sealing cover is connected to the dust removal air net every 2 meters, and 4 dust removal ports are set on the cleaning screen to connect with the centralized dust removal air network. The centralized dust removal system adopts the fan-discharger-dust collector. -The combination of chimneys can achieve no dust in the workshop, and the 15-meter-high spiral galvanized pipe of the dust-removing chimney, the motor has explosion-proof function, and the alarm function of fire danger is set, so that the indoor dust concentration is lower than 10mg/m3, and the outdoor dust concentration is lower than 150mg/ m3.
(5) Set up a number of fiber raw material weighing bins, each with a volume of 35 cubic meters, weight reduction, and box material: Q345. Box material thickness Bottom plate thickness ≥ 4mm Side plate thickness ≥ 3mm
Power: 15Kw/piece, box body 16Mn material, scraper chain conveyor mechanism heavy-duty conveyor chain. Set up multiple silage bins, the volume is 50m3, the box material is 304 stainless steel, the external Q235 material frame, power: 30Kw/piece, the thickness of the 304 stainless steel anti-corrosion material of the box body is ≥ 2.5mm, the thickness of the stainless steel anti-corrosion auger blade> 4mm, the stirring The number of dragons is ≥2, and the scraper chain conveyor mechanism is heavy-duty conveyor chain.
After pretreatment, the clean segment enters the weighing bin, and after being accurately weighed, it enters the TMR machine through the transfer belt conveyor.
Enter the TMR machine through the transfer belt conveyor.
-
The whole system is divided into rope unwinding section - bundling section - cleaning section - dust removal section - (crushing section)
-
For more product details: please call 15993745555
Working Principle
-
- Commodity name: Straw Pretreatment System
- Production capacity: 5-20t/h
- Applicable materials: feed fiber, etc.
- Applications: pasture, etc.
The straw pretreatment system undertakes 70% of the raw material processing tasks in the total mixed ration. Due to the small volume, large volume, many types of fibrous raw materials, complex impurities, and easy generation of dust, the supercritical value of dust concentration has the characteristics of the danger of electrostatic explosion, etc. , is the bottleneck for the realization of intelligent operation in the central kitchen of the pasture. In the cost of ruminant forage, the cost control of fiber raw materials is an important element of competition among ruminant breeding enterprises.
The whole system is divided into rope unwinding section - bundling section - cleaning section - dust removal section - (crushing section)
(1) Unpacking machine: The unpacking machine realizes the separation of the foreskin and the straw bale through continuous actions such as cutting the foreskin - hooking the foreskin - collecting the foreskin.
(2) Bale breaking section: baling straw (small square bales, large square bales, secondary pressure square bales, garden bales), first put the straw bales on the plate chain conveyor platform through the grass grabber, and pass the No. 1 plate The chain conveyor 1 is frequency-converted and conveyed to the unroping mechanism, and the tie rope and nylon net rope are cut out, and the rope is collected through the bypass.
The bundled straw with the rope cut off enters the baler breaker. The baler breaks the straw to a particle size of 30-40 mm, and is sent to the next section by the No. 2 plate chain conveyor. The circuit design adopts a frequency conversion motor.
Screening and cleaning section: The straw segment is transported to the screening and cleaning section through the plate chain conveyor. There are mainly straw cleaning screens, fans, pulse dust collectors, air locks, No. 3 plate chain conveyors, permanent magnet self-unloading type dust collectors Iron and other equipment.
(3) After the broken straw segment is broken, the iron-containing material is first removed by a permanent magnet self-unloading iron remover, and high-strength rare earth NdFeB is used to form a strong magnetic core, which has a strong magnetic field and a high magnetic field gradient, and the conveyor belt conveys The material and iron removal can realize continuous iron absorption and abandonment. The belt has automatic deviation correction function, reliable operation and simple maintenance. Its internal magnetic circuit adopts a perfect magnetic pole structure to ensure that the whole machine can operate without failure for a long time in harsh environments. Explosion-proof type, Magnetic plate strength 150MT, cleaning 0.1-30 kg of ferromagnetic material,
The No. 3 plate chain conveyor sends the straw segments into the straw cleaning screen. There are 4 different screen mesh working surfaces in the cleaning screen. The materials entering the trommel screen follow different trajectories through different specific gravity, and cannot pass through the screen due to different external dimensions. The corresponding outlet can clean up the dust and fine gravel in the straw. Auxiliary dust removal equipment system can handle the dust generated during the screening process. Fans, pulse dust collectors and air closers form an effective dust removal air network.
(4) Dust removal system: the top of the No. 1 chain conveyor is connected to the centralized dust removal air net by installing a sealing leather curtain.
The number plate chain conveyor is fully sealed, the air outlet on the sealing cover is connected to the dust removal air net every 2 meters, and 4 dust removal ports are set on the cleaning screen to connect with the centralized dust removal air network. The centralized dust removal system adopts the fan-discharger-dust collector. -The combination of chimneys can achieve no dust in the workshop, and the 15-meter-high spiral galvanized pipe of the dust-removing chimney, the motor has explosion-proof function, and the alarm function of fire danger is set, so that the indoor dust concentration is lower than 10mg/m3, and the outdoor dust concentration is lower than 150mg/ m3.
(5) Set up a number of fiber raw material weighing bins, each with a volume of 35 cubic meters, weight reduction, and box material: Q345. Box material thickness Bottom plate thickness ≥ 4mm Side plate thickness ≥ 3mm
Power: 15Kw/piece, box body 16Mn material, scraper chain conveyor mechanism heavy-duty conveyor chain. Set up multiple silage bins, the volume is 50m3, the box material is 304 stainless steel, the external Q235 material frame, power: 30Kw/piece, the thickness of the 304 stainless steel anti-corrosion material of the box body is ≥ 2.5mm, the thickness of the stainless steel anti-corrosion auger blade> 4mm, the stirring The number of dragons is ≥2, and the scraper chain conveyor mechanism is heavy-duty conveyor chain.
After pretreatment, the clean segment enters the weighing bin, and after being accurately weighed, it enters the TMR machine through the transfer belt conveyor.
Enter the TMR machine through the transfer belt conveyor.
-
The whole system is divided into rope unwinding section - bundling section - cleaning section - dust removal section - (crushing section)
-
For more product details: please call 15993745555
Technical parameters
-
- Commodity name: Straw Pretreatment System
- Production capacity: 5-20t/h
- Applicable materials: feed fiber, etc.
- Applications: pasture, etc.
The straw pretreatment system undertakes 70% of the raw material processing tasks in the total mixed ration. Due to the small volume, large volume, many types of fibrous raw materials, complex impurities, and easy generation of dust, the supercritical value of dust concentration has the characteristics of the danger of electrostatic explosion, etc. , is the bottleneck for the realization of intelligent operation in the central kitchen of the pasture. In the cost of ruminant forage, the cost control of fiber raw materials is an important element of competition among ruminant breeding enterprises.
The whole system is divided into rope unwinding section - bundling section - cleaning section - dust removal section - (crushing section)
(1) Unpacking machine: The unpacking machine realizes the separation of the foreskin and the straw bale through continuous actions such as cutting the foreskin - hooking the foreskin - collecting the foreskin.
(2) Bale breaking section: baling straw (small square bales, large square bales, secondary pressure square bales, garden bales), first put the straw bales on the plate chain conveyor platform through the grass grabber, and pass the No. 1 plate The chain conveyor 1 is frequency-converted and conveyed to the unroping mechanism, and the tie rope and nylon net rope are cut out, and the rope is collected through the bypass.
The bundled straw with the rope cut off enters the baler breaker. The baler breaks the straw to a particle size of 30-40 mm, and is sent to the next section by the No. 2 plate chain conveyor. The circuit design adopts a frequency conversion motor.
Screening and cleaning section: The straw segment is transported to the screening and cleaning section through the plate chain conveyor. There are mainly straw cleaning screens, fans, pulse dust collectors, air locks, No. 3 plate chain conveyors, permanent magnet self-unloading type dust collectors Iron and other equipment.
(3) After the broken straw segment is broken, the iron-containing material is first removed by a permanent magnet self-unloading iron remover, and high-strength rare earth NdFeB is used to form a strong magnetic core, which has a strong magnetic field and a high magnetic field gradient, and the conveyor belt conveys The material and iron removal can realize continuous iron absorption and abandonment. The belt has automatic deviation correction function, reliable operation and simple maintenance. Its internal magnetic circuit adopts a perfect magnetic pole structure to ensure that the whole machine can operate without failure for a long time in harsh environments. Explosion-proof type, Magnetic plate strength 150MT, cleaning 0.1-30 kg of ferromagnetic material,
The No. 3 plate chain conveyor sends the straw segments into the straw cleaning screen. There are 4 different screen mesh working surfaces in the cleaning screen. The materials entering the trommel screen follow different trajectories through different specific gravity, and cannot pass through the screen due to different external dimensions. The corresponding outlet can clean up the dust and fine gravel in the straw. Auxiliary dust removal equipment system can handle the dust generated during the screening process. Fans, pulse dust collectors and air closers form an effective dust removal air network.
(4) Dust removal system: the top of the No. 1 chain conveyor is connected to the centralized dust removal air net by installing a sealing leather curtain.
The number plate chain conveyor is fully sealed, the air outlet on the sealing cover is connected to the dust removal air net every 2 meters, and 4 dust removal ports are set on the cleaning screen to connect with the centralized dust removal air network. The centralized dust removal system adopts the fan-discharger-dust collector. -The combination of chimneys can achieve no dust in the workshop, and the 15-meter-high spiral galvanized pipe of the dust-removing chimney, the motor has explosion-proof function, and the alarm function of fire danger is set, so that the indoor dust concentration is lower than 10mg/m3, and the outdoor dust concentration is lower than 150mg/ m3.
(5) Set up a number of fiber raw material weighing bins, each with a volume of 35 cubic meters, weight reduction, and box material: Q345. Box material thickness Bottom plate thickness ≥ 4mm Side plate thickness ≥ 3mm
Power: 15Kw/piece, box body 16Mn material, scraper chain conveyor mechanism heavy-duty conveyor chain. Set up multiple silage bins, the volume is 50m3, the box material is 304 stainless steel, the external Q235 material frame, power: 30Kw/piece, the thickness of the 304 stainless steel anti-corrosion material of the box body is ≥ 2.5mm, the thickness of the stainless steel anti-corrosion auger blade> 4mm, the stirring The number of dragons is ≥2, and the scraper chain conveyor mechanism is heavy-duty conveyor chain.
After pretreatment, the clean segment enters the weighing bin, and after being accurately weighed, it enters the TMR machine through the transfer belt conveyor.
Enter the TMR machine through the transfer belt conveyor.
-
The whole system is divided into rope unwinding section - bundling section - cleaning section - dust removal section - (crushing section)
-
For more product details: please call 15993745555
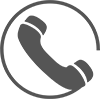
Tel:
Related Equipment
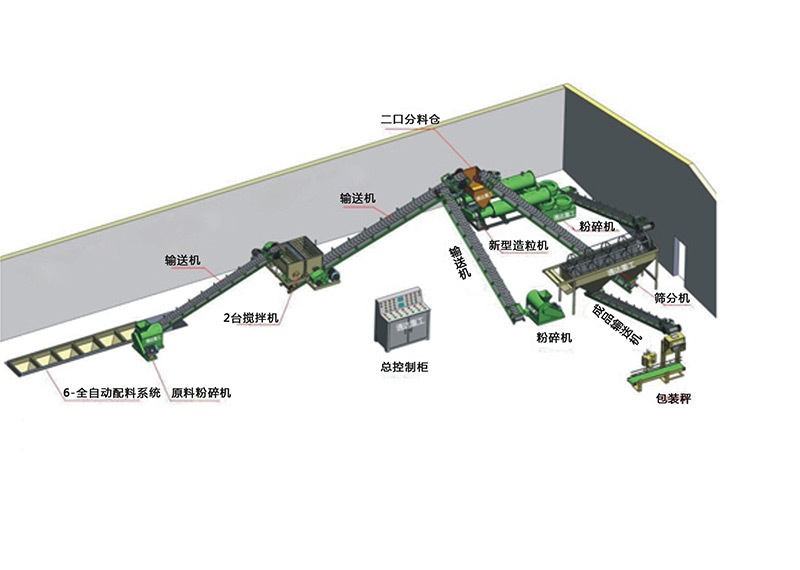
Organic fertilizer production line

Slag name
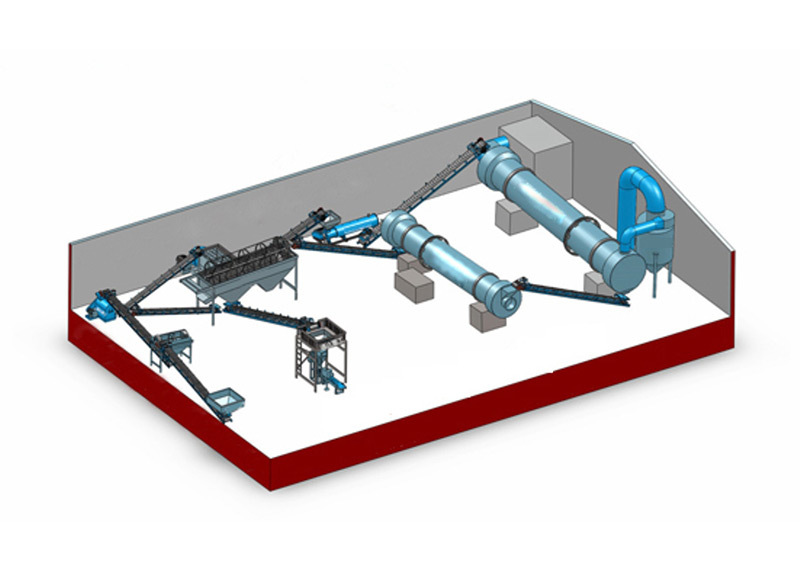
Organic fertilizer and detailed text
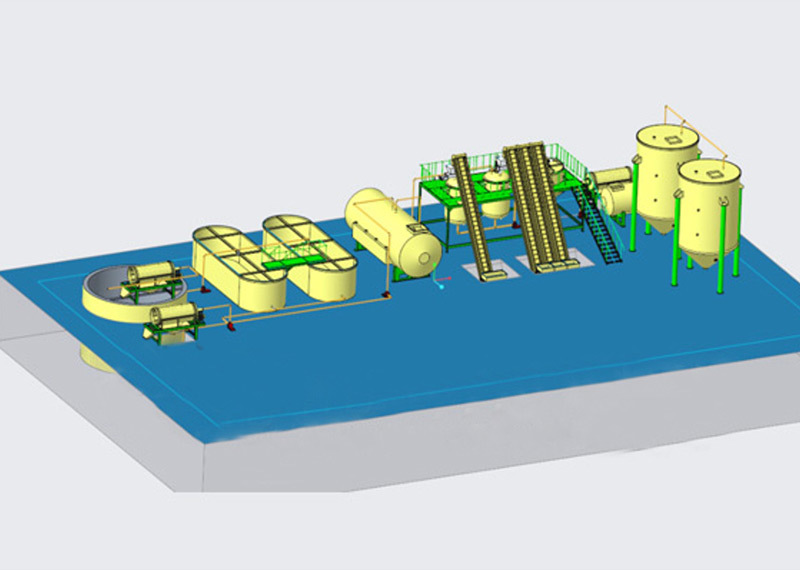
Water soluble fertilizer
Inquiry